Tobacco’s legacy is visible in every corner of North Carolina, from greenways and campuses to smokestacks imprinted with the industry’s biggest names. In many ways, North Carolina was built on tobacco. But when the Surgeon General announced the link between tobacco and certain cancers in 1964, tobacco farmers across the country, and in our state especially, felt a drop in demand that they’ve been feeling ever since. Even though North Carolina remains by far the country’s largest tobacco producer, many current and former growers have been searching for alternatives.
Enter the alternative crops Extension program led by David Suchoff, an assistant professor in the Department of Crop and Soil Sciences at North Carolina State University.
“Tobacco was the perfect storm in terms of being very high quality with a very high demand,” Suchoff says. “For that reason, I always tell people that we are probably never going to find the next tobacco for North Carolina.”
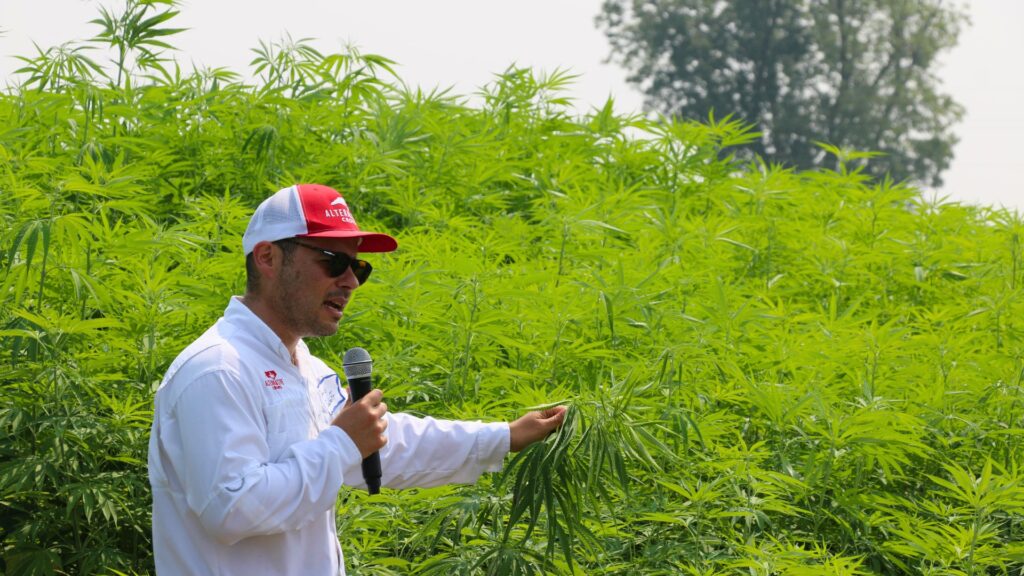
Photo credit: Simon Gonzalez
But Suchoff’s program is working diligently to find something that comes close–an economically viable crop with durable market demand and decent margins that farmers can fit into existing production systems.
“One of the four guiding principles of the alternative crops program is that the crop has to have a market. We could look at all kinds of weird stuff, but if there’s no market, it’s no good to the farmer,” Suchoff says.
While his program works on a variety of crops as alternatives for far more than just tobacco, his most recent funding is looking into how fiber hemp can act as an alternative for farmers moving away from the broad-leafed cash crop.
Finding the Sweet Spot
The current five-year grant seeks to address survey results from existing fiber hemp farmers who shared their biggest challenges with the crop: planting density, weed management and fertility.
In order to get high-quality fiber, the plant’s stems need to be tall and thin. This means farmers have to plant a lot of seeds very close together. But because seeds are expensive, it’s important to find the sweet spot that balances input costs, fiber quality and yield. Suchoff’s planting density studies are searching for that sweet spot while also solving for weed pressure and fertility.
Because hemp seeds are planted so close together, farmers lack the ability to till with traditional methods. Suchoff and his team are conducting planting date studies, with preliminary results indicating that hemp can be planted as early as mid-March to help beat out the pesky Palmer amaranth that pops up in May. They are also testing cover crop mulch in a no-till system to help suppress weeds during the early growth stage.
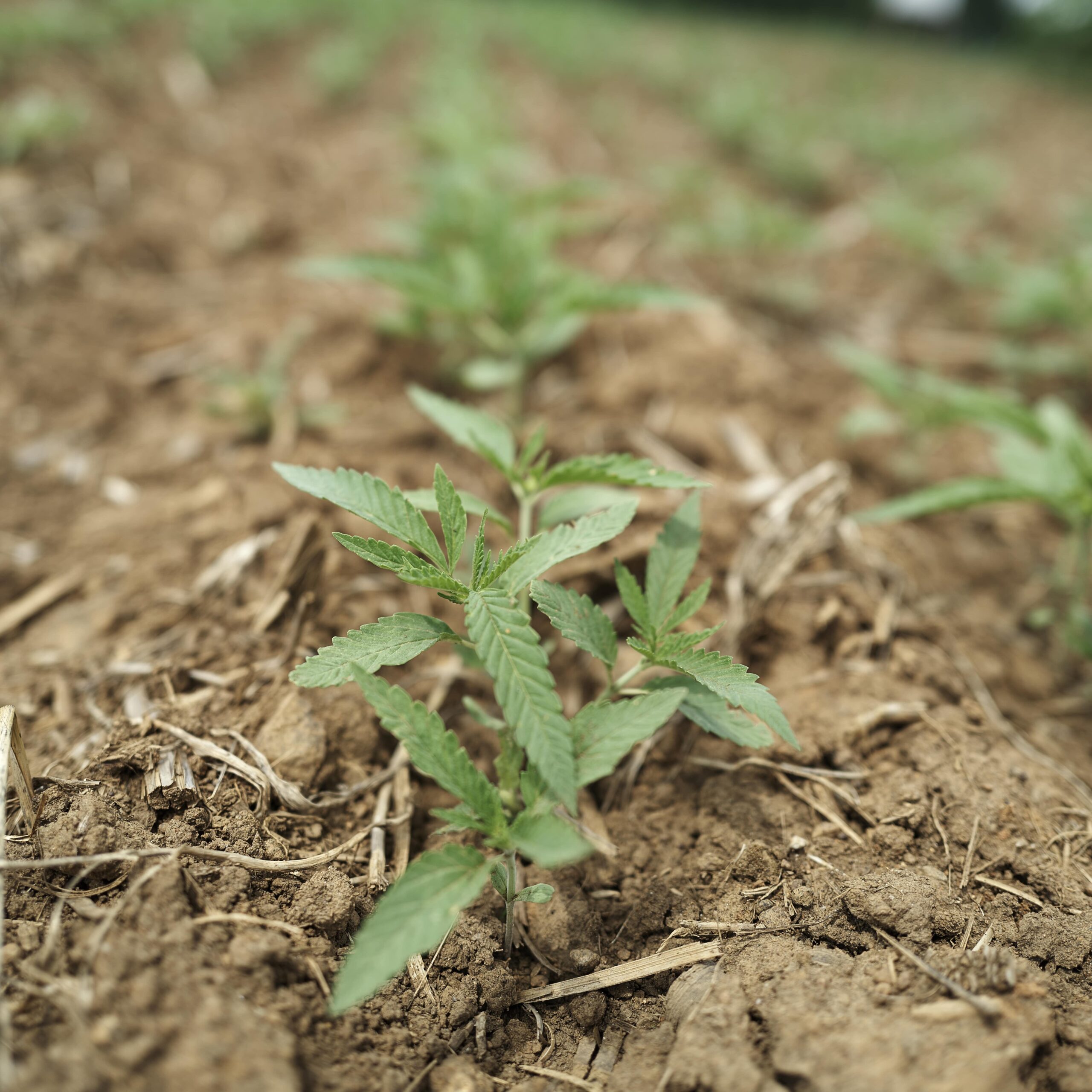
In addition to helping with weed management, cover crops are also being tested as a nitrogen source, which plants need for growth. Leguminous cover crops like hairy vetch are incorporated at varying levels with an increasing nitrogen rate study to find the sweet spot for yield and input costs.
We could look at all kinds of weird stuff, but if there’s no market, it’s no good to the farmer.
Suchoff and his team are also working on breeding domestic varieties that fit North Carolina’s latitude. As a day-length sensitive crop, hemp only grows stems and leaves if the days are longer than the critical day-length period. Day lengths below that threshold will signal the plant to start flowering and stop growing, which is exactly what happens when the common fiber hemp varieties from northern latitudes like Canada are brought further south.
“We’re working with Cornell University through the FFAR Hemp Research Consortium to develop varieties that are a better fit for the Southeast and that do not produce THC,” Suchoff says.
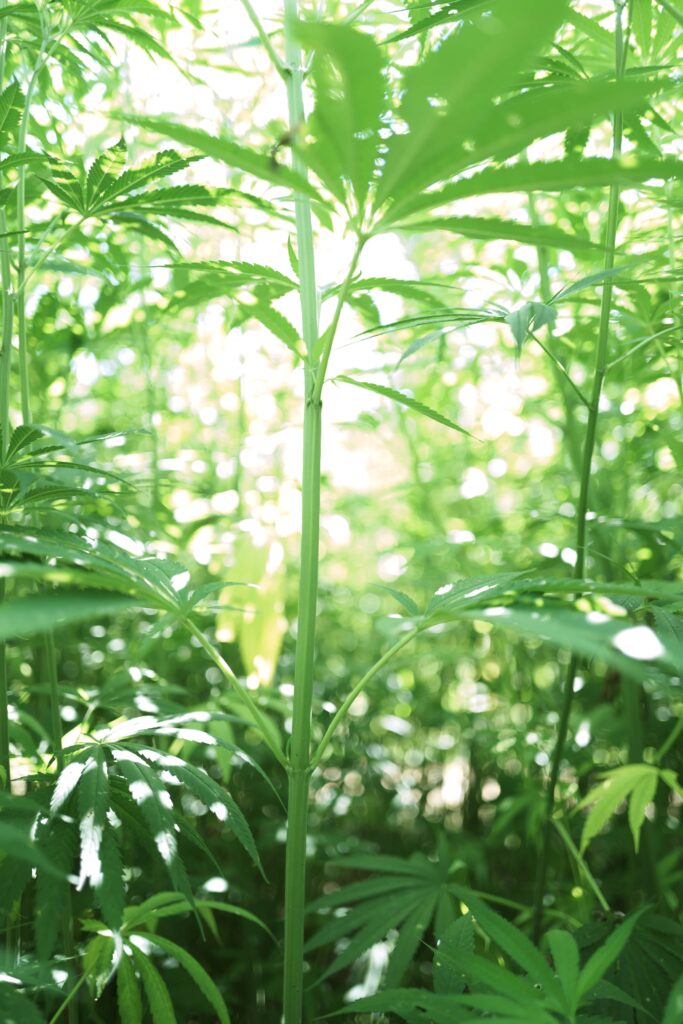
Lastly, Suchoff is studying various harvest methods. Harvest timing depends on maximizing fiber while minimizing lignin so that processors get enough quality fiber from each plant. At harvest, the crop is cut and left in the field to break down during a process called retting. During retting, microbes in the environment break down pectin, a gluey substance binding the woody stem and the eventual fiber together. But letting it ret for too long or not long enough will render the stems either unprocessable or actually degrade the fibers, so Suchoff is conducting retting studies to find the sweet spot. Once retting is complete, the hemp is baled like hay and sent to the next phase of its journey.
Row Crop to Crop Top
“One of the bigger challenges that we’ve had with fiber hemp is that it requires a number of processing steps to get it from its raw form in the field to something that could eventually be spun,” Suchoff says.
The first step for processing fiber hemp is called decortication, which separates the bast from the hurd by crushing the stems through rollers. The bast is the green outer bark on the stem, where the long, strong fibers are located that are used for textiles. The hurd is the inner woody core of the stem.
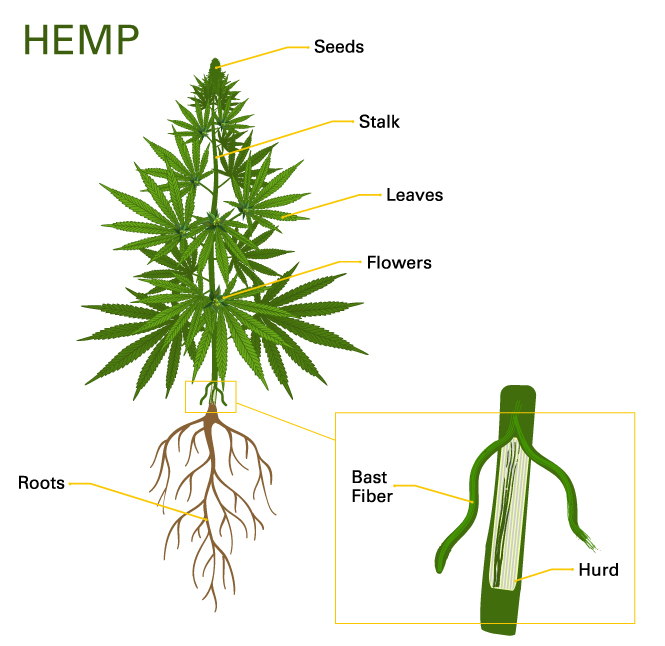
“The second step is called degumming,” Suchoff explains. “You take your bast fiber, which looks like a ribbon, and you cook it with either acids or bases or high pressure. In this step, you’re getting rid of lignin and cellulose and all these other compounds you don’t need so that you’re just left with those pure fibers that can then be spun and woven.”
North Carolina is currently the only state in the country with both a decorticator and a degummer, which gives North Carolina-grown fiber hemp a significant competitive advantage. This edge is largely thanks to North Carolina’s long history as a textile state.
The Fabricated Fate of Fiber Hemp
Alongside tobacco, the textile industry dominated North Carolina’s economy in the 19th and 20th centuries and remains a strong industry today. A recent study from NC State’s Wilson College of Textiles (the only textile college in North America) found that North Carolina has 25% of the country’s textile employees and accounts for 20% of the country’s textile exports. The beauty of growing fiber hemp in North Carolina is that the textile industry’s unique infrastructure is already in place to support a circular economy from field to fabric. Many large, well-established companies are interested in using fiber hemp to make everything from pants to paper.

“Where you see a lot of fiber hemp is in cotton fiber blends like denim, canvas and jackets. The industry gets excited when they see fiber hemp as a replacement for a lot of the synthetics that are in cotton synthetic blends, and that’s a sustainability story,” Suchoff says. “But fiber hemp is not going to replace cotton. It is a very different fiber and feels different on the skin.”
Suchoff is collaborating with faculty in the Wilson College of Textiles to ensure that the fiber hemp in the field translates to hemp fibers the textile industry wants. They are also working on establishing a grading system for fiber hemp that would create much-needed quality standards where none currently exist for dictating farmgate prices, preferred varieties and agronomic practices.
“The industry gets excited when they see fiber hemp as a replacement for a lot of the synthetics that are in cotton synthetic blends, and that’s a sustainability story.”
While fiber hemp may or may not become the next tobacco, it has all the makings to become a uniquely North Carolinian crop. With help from Suchoff and the entire alternative crops Extension program, North Carolina fiber hemp may soon appear in closets all across the country.
This post was originally published in Plant Sciences Initiative.
- Categories: